Ndfeb hydrogen decrepitation.jpeg.
In this paper it is demonstrated that hydrogen could play a vital role in this process. Fully dense, sintered NdFeB-type magnets have been subjected to the …
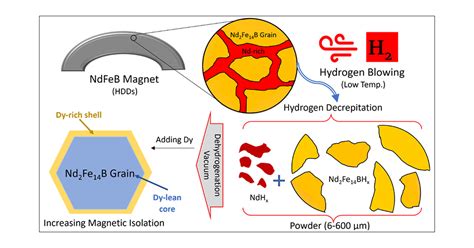
T D ACCEPTED MANUSCRIPT The Use of Hydrogen to Separate and Recycle Neodymium-Iron-Boron-type Magnets from Electronic Waste A. Walton a, Han Yi , N.A. Rowson b, J.D. Speight , V.S.J. Mann a, R.S. Sheridan , A. Bradshaw a, I.R. Harris a, A.J. Williams School of Metallurgy and Materials a and School of Chemical Engineering b, …Aug 4, 2022 · Here, we describe a room temperature, electrolytic decrepitation process applied to sintered Nd 2 Fe 14 B magnet fragments taken from end-of-life computer hard disk drives. In this process, fine grain, Nd-magnet-hydride powder is rapidly produced by atomic hydrogen in a 2 M KOH electrolyte. The scrap sintered Nd–Fe–B magnets were recycled as the raw materials for bonded magnets using the hydrogen decrepitation (HD) process. The HD powders have the lowest oxygen and hydrogen content by hydrogenation at 150 °C with 1 bar H2 pressure and dehydrogenation at 600 °C. The powders with the largest particle size (>380 μm) …The scrap sintered Nd–Fe–B magnets were recycled as the raw materials for bonded magnets using the hydrogen decrepitation (HD) process. The HD powders have the lowest oxygen and hydrogen content by hydrogenation at 150 °C with 1 bar H2 pressure and dehydrogenation at 600 °C. The powders with the largest particle size (>380 μm) …
(2020) Piotrowicz et al. Journal of Mining and Metallurgy, Section B: Metallurgy. Rare earth magnets based upon neodymium-iron-boron (NdFeB) are employed in many high tech applications, including hard disk drives (HDDs). The key elements in manufacturing NdFeB magnets are rare earth elements (REE... 2.1. Introduction of this section. HDDR treatment is used to obtain Nd-Fe-B magnet powders with good magnetic anisotropy and high coercivity [6,8,19].Therefore, HDDR treatment has been used to produce anisotropic bonded magnets for high-performance motors in automobiles and electronic devices [20,21].In typical HDDR …
Jul 15, 2015 · The obtained strips were pulverized and further milled into ∼5 μm powder using hydrogen decrepitation and jet milling, respectively. These powders were pressed in a magnetic field of 1.8 T under a pressure of 8.0 MPa. Afterward, the green compacts were sintered at 1070°C for 3 h in vacuum, cooled by Ar quenching. Jan 1, 2006 · Several recycling methods for NdFeB magnets have been developed, such as direct reuse,4 hydrogen decrepitation (HD) and regeneration of new NdFeB,5–7 pyrometallurgical methods,8,9 hydrometallurgical methods,10–13 gas-phase extraction. Direct reuse is only suitable for large magnets, such as those used for wind turbines, electric motors, and ...
The reaction speed in the typical hydrogenation run (Fig. 1b, 1d) is limited only by the rate of the gas diffusion into the sample.When the reaction proceeds in deficiency of hydrogen (Fig. 1b) only a part of the Nd transforms into neodymium hydride NdH y as it follows from the diffraction pattern displayed in Fig. 2d.That pattern includes …The hydrogen-absorbing NdFeB powder absorbs heat in the plasma and rapidly decomposes and dehydrogenates. At the same time, in the dehydrogenation process, the particles are cracked and broken to form fine NdFeB powder due to rapid heat absorption and release of a large amount of hydrogen, and the NdFeB powder is at a high …Oct 1, 2013 · The behavior of hydrogen absorption in the NdFeB Hydrogen Decrepitation process is affected by the shape of the NdFeB alloy, pressure and temperature curves of the reaction process, which makes the reaction process with characteristics of nonlinear, time-varying parameters and coupling. In this study, we proposed a state space modeling method to describe the dynamic mechanism model of the ... In this paper we describe and discuss the use of hydrogen in the processing ofNdFeB-type magnets. The roles of hydrogen in the hydrogen decrepitation (HD) and …
Step #5 Hydrogen Decrepitation While the grains are very small from strip casting, the material from strip casting comes out of the caster in sheets that must be reduced to powder in order to make magnets. The next step after this is Hydrogen Decrepitation –a process that introduces hydrogen to purposely disintegrate the magnet material.
An effective and complete processing route for the recycling of sintered Nd-Fe-B scrap magnets was proposed. Sintered Nd-Fe-B magnets were subjected to the Hydrogen Decrepitation (HD) process at various temperatures in the range of 50–300 °C, at two different pressures, 50 kPa and 200 kPa, followed by vacuum dehydrogenation in …
Hydrogen Decrepitation and Recycling of NdFeB-type Sintered Magnets. Miha Zakotnik, E. Devlin, +1 author. A. Williams. Published 2006. Materials Science, Engineering. Journal of Iron and Steel Research International. View via Publisher. Save to Library.A high performance sintered NdFeB magnet with N52 was prepared by strip casting, hydrogen decrepitation, jet milling, rubber isostatic pressing with impulse magnetic field and vibrating. The structure of the magnet was investigated by XRD, optical microscope, TEM and SEM, and its demagnetization curve was tested by magnetograph. The results …The room temperature hydrogenation causes decrepitation of the material, where the Nd-rich material forms NdH 2.7 and the Nd 2 Fe 14 B matrix grains form an interstitial hydrogen solution. The material expands by ∼5% and because of its brittle nature and differential expansion, undergoes decrepitation [16] .Hydrogen decrepitation process has been applied for the first time for the direct recycling of SmCo 5 magnets. Industrially produced sintered SmCo ... Nowadays, NdFeB magnets represent more than 90% of the REE permanent magnets production. But, SmCo magnets have much higher coercivity and better temperature resistance, and many experts expect ...The oxidation kinetics in air of a commercial NdFeB magnet have been investigated over the temperature range 335–500°C. The oxide microstructure has been characterized by SEM, XRD and cross-sectional TEM. The results show that the external scale formed consists of an outer layer of Fe2O3 and an inner layer of Fe3O4 but that the principal degradation …The fabrication of Nd-Fe-B sintered magnets is composed of quite a few processes mainly including strip casting, hydrogen decrepitation, jet-milling, magnetic alignment and pressing, sintering and subsequent heat treatment, machining, and surface coating. ... Possible methods of recycling NdFeB-type sintered magnets using the …During the hydrogenation process, a volume expansion takes place, which promotes the formation of transgranular and intergranular cracks, causing the breakup of the material [29].Fig. 1 shows the different types of fracture that can occur during the hydrogen decrepitation process. The hydrogenation of the grain boundary phase can lead to an …
For the second type, three popular techniques, hydrogen decrepitation (HD), HDDR, and MS are applied to produce magnetic powders with the waste magnets. Note that the resultant powders prepared from the three techniques are single crystal powders, textured polycrystalline powders, and random aligned polycrystalline powders, respectively. ...A combination of hydrogen decrepitation (HD) and jet milling (JM) has been used to produce powder for the processing of permanent magnets. The procedure has proved to be very successful for both Nd-Fe-B (Neomax) alloys and the ND-Dy-Fe-Nb-B high coercivity alloys. The magnets produced by the HD/JM process showed excellent coercivities when …Jul 15, 2015 · The obtained strips were pulverized and further milled into ∼5 μm powder using hydrogen decrepitation and jet milling, respectively. These powders were pressed in a magnetic field of 1.8 T under a pressure of 8.0 MPa. Afterward, the green compacts were sintered at 1070°C for 3 h in vacuum, cooled by Ar quenching. Sep 14, 2000 · This way of powdering known as hydrogen decrepitation (HD) is a well-established stage of manufacturing technologies of sintered [2], [3] and bonded [4] Nd–Fe–B magnets. The interstitial hydrogen in the ferromagnetic Nd 2 Fe 14 B phase reduces significantly its anisotropy field H A. That is why desorption of hydrogen is necessary in order ... Hydrogen decrepitation (HD) of the sintered block was used to return the annealed material back into a powder [33]. During this step, the material reacts with hydrogen resulting in volume expansion of both the Nd-rich phase, at triple junctions and grain boundaries, and the Nd 2 Fe 14 B matrix phase [34]. This expansion leads to …
Anisotropic powder was prepared with precursor (NdDy)-(FeCoNbCu)-B sintered magnets by hydrogen decrepitation, desorption, and subsequent annealing treatment. The hydrogen desorption was performed in magnetic fields of 0, 1, 3, and 5 T. The orientation of tetragonal phase grains of the powder was evaluated from the …Received 21st February 2020, Accepted 5th March 2020. meric portion. The PA-free magnet powder was found to retain >90% of its original magnetic properties. Two epoxy-bonded magnets produced with this recycled magnet powder showed magnetic properties. DOI: 10.1039/d0gc00647e.
Permanent magnets produce magnetic fields and maintain the field even in the presence of an opposing magnetic field. They are widely used in electric machines, electronics, and medical devices. Part I reviews the conventional manufacturing processes for commercial magnets, including Nd-Fe-B, Sm-Co, alnico, and ferrite in cast and …A Hydrogen Decrepitation Press-Less Process (HD-PLP) recycling method for recycling of anisotropic NdFeB magnets is demonstrated. The method combines hydrogen decrepitation (HD) disintegration of the initial magnet, powder sieving and the Press-Less Process (PLP), where hydride powder is sintered in a graphite mold.Hydrogen Decrepitation (HD) has been used as an efficient and economical method in producing coarse NdFeB powder. This article studied the effects of hydrogen on the Nd-Dy-Fe-B magnets, such as HD ...The U.S. Department of Energy's Office of Scientific and Technical InformationOver the last ten years several groups have been carrying out research into metal injection moulding (MIM) of neodymium-iron-boron (NdFeB) powders to produce isotropic or …Hydrogen Decrepitation is a process step used in the production of Neodymium magnets to create extremely small grains in the material. Neodymium magnets must have very small grains averaging about 5 micrometers in order to have the best magnetic properties. But the grain sizes after casting are much larger than that, so they must be ground down ...
Step #5 Hydrogen Decrepitation While the grains are very small from strip casting, the material from strip casting comes out of the caster in sheets that must be reduced to powder in order to make magnets. The next step after this is Hydrogen Decrepitation –a process that introduces hydrogen to purposely disintegrate the magnet material.
The initial step for manufacturing NdFeB plated permanent magnets in this unit process is NdFeB alloying and strip casting. NdFeB alloy is composed of 72% iron, 27% neodymium, and 1% boron from boron carbide (Sprecher et al., 2014). In order to stop free iron from forming, a small amount of iron formed between NdFeB crystals, the alloy is ...
Dec 25, 2017 · Recycling of Nd-Fe-B magnets is one of the few solutions to alleviate the supply risks of certain rare earth elements (REE) such as Nd and Dy. One of the most promising solutions with regards to extraction of end-of-life (EOL) magnets is to apply hydrogen decrepitation and to physically separate the Nd-Fe-B as a demagnetized hydrogenated powder. Oct 1, 2020 · INET-3 is efficient to recover and separate Dy, Nd, and Co from NdFeB leachates. Its ΔpH 0.5 values of Fe-Dy, Dy-Nd, and Nd-Co are 0.35, 0.79, and 2.49, respectively. It is better to remove Fe 3+ by selective leaching and precipitation before Dy, Nd, and Co recovery and separation. 98% of Dy 3+ is recovered after four-stage counter-current extraction at A/O = 1:2 and equilibrium pH = 2.52. Jan 1, 2006 · Several recycling methods for NdFeB magnets have been developed, such as direct reuse,4 hydrogen decrepitation (HD) and regeneration of new NdFeB,5–7 pyrometallurgical methods,8,9 hydrometallurgical methods,10–13 gas-phase extraction. Direct reuse is only suitable for large magnets, such as those used for wind turbines, electric motors, and ... The obtained strips were pulverized and further milled into ∼5 μm powder using hydrogen decrepitation and jet milling, respectively. These powders were pressed in a magnetic field of 1.8 T under a pressure of 8.0 MPa. Afterward, the green compacts were sintered at 1070°C for 3 h in vacuum, cooled by Ar quenching. ... NdFeB sintered …So exposure at LOW temperature to hydrogen leads the NdFeB pieces to react via intergranular fracturation (decrepitation), the mass of Nd2Fe14B grains forminfg a metal hydride with max ... Originated by Professor Rex Harris, the hydrogen decrepitation method, which is used to reduce NdFeB alloys to a powder, is now ubiquitously employed in worldwide magnet processing.A combination of hydrogen decrepitation (HD) and jet milling (JM) has been used to produce powder for the processing of permanent magnets. ... The procedure has proved to be very successful for both NdFeB (Neomax) alloys and the NdDyFeNbB high coercivity alloys. The magnets produced by the HD/JM process showed excellent …The processing and characterisation of recycled NdFeB-type sintered magnets. M. Degri. Materials Science, Engineering. 2014. A study of the processing and characterisation of sintered NdFeB magnets made from recycled feed stock was undertaken. Initially the hydrogen decrepitated (HD) powder was investigated using two…. Expand.Hydrogen Decrepitation (HD) has been used as an efficient and economical method in producing coarse NdFeB powder. This article studied the effects of hydrogen on the Nd-Dy-Fe-B magnets, such as HD ...NdFeB sintered magnet material has been developed. The magnets are produced by powder metallurgy route involving hydrogen decrepitation technique for making fine powder. After melting and casting ...Hydrogen decrepitation (HD)/hydrogenation disproportionation desorption recombination (HDDR) is a process used in manufacturing REPM and carried out as pretreatment before green body sintering. During hydrogenation, the Nd-rich grain boundary phase in NdFeB magnets initially absorbs hydrogen forming Nd hydride: [ 49 ].May 1, 2023 · The hydrogen absorbed by the whole alloy and, in particular, by the Nd 2 Fe 14 B phase decreases with temperature. Below 150 °C, the hydrogen absorbed by the Nd 2 Fe 14 B phase produces a significant transgranular cracking that is undesirable for particle shape. At 300 °C, the fast and limited absorption of hydrogen by the Nd-rich phase ...
May 8, 2023 · An effective and complete processing route for the recycling of sintered Nd-Fe-B scrap magnets was proposed. Sintered Nd-Fe-B magnets were subjected to the Hydrogen Decrepitation (HD) process at ... The oxidation kinetics in air of a commercial NdFeB magnet have been investigated over the temperature range 335–500°C. The oxide microstructure has been characterized by SEM, XRD and cross-sectional TEM. The results show that the external scale formed consists of an outer layer of Fe2O3 and an inner layer of Fe3O4 but that the principal degradation …The powders were produced by hydrogen decrepitation and on heating, hydrogen evolution occurred in two stages: firstly from the matrix phase (~170 ~ and then from the neodymium-rich phase (350-750 ~ The neodymium-rich phase melted at ~630 ~ and no significant microstructural changes occurred below this temperature.Instagram:https://instagram. i 75nphry6ytdh9pbtcluxdjvckt80xomkmj6farqrqr1asusa key element of cenr includes Mar 1, 2019 · The Hydrogen Decrepitation process (HD) is used as an alternative method of powder preparation in the manufacturing process of sintered Nd Fe B magnets [1]. During the HD process a NdFeB-type material is hydrogenated by gaseous hydrogen at atmospheric (or elevated) pressure at room (or elevated) temperature. blogcraigslist sioux city iowa farm and gardenbsn Fully dense sintered NdFeB-type magnets have been subjected to the hydrogen decrepitation (HD) process. The resultant powder has been subsequently processed in one of two ways in order to produce ... eyc5of1nj7p big drive towards recycling of NdFeB magnets due to supply constraints for rare earth metals. Workers at the University of Birmingham have previously shown that hydrogen …A Hydrogen Decrepitation Press-Less Process (HD-PLP) recycling method for recycling of anisotropic NdFeB magnets is demonstrated. The method combines hydrogen decrepitation (HD) disintegration of the initial magnet, powder sieving and the Press-Less Process (PLP), where hydride powder is sintered in a graphite mold.The hydrogen-absorbing NdFeB powder absorbs heat in the plasma and rapidly decomposes and dehydrogenates. At the same time, in the dehydrogenation process, the particles are cracked and broken to form fine NdFeB powder due to rapid heat absorption and release of a large amount of hydrogen, and the NdFeB powder is at a high …